|
Post by technidiver on Jun 27, 2019 15:31:45 GMT -8
|
|
|
Post by SeaRat on Jun 27, 2019 16:13:47 GMT -8
TD, Yes, I used them in the U.S. Naval School for Underwater Swimmers in 1967.  The best thing to do is to read what Bill High said about these cylinders: Here are some more photos of these tanks:  Bob Means, my dive buddy and follow Pararescue trainee, on a compass course. Note the U.S. Navy aluminum tanks.  Our exit point on a Key West, Florida beach. Some of the Navy guys got turned around, and were headed to Cuba before the boat pulled their float and brought them up, turned them around so that they were headed to the beach. Now, the reason they are not to be hydrostatic retested or filled is that their bottom was made by a different process. They were non-magnetic, and used by the UDT, especially for work out of submarines and with magnetic mines. They were 3000 psig tanks, with a full capasity of 90 cubic feet. They were used only as doubles in the Navy, and the Navy traded USAF PJs for our jump tanks (40 cubic feet doubles) at times, as these tanks are really heavy. Here's the photo from E-Bay of the bottom, and if you will look it appears that there is a crack. The bottom plug is why these were never meant to be re-tested by hydro. (Note--this is disputed by Luis) When I was in Roseburg, Oregon as a safety and health consultant, I got word that a school in the south of Douglas County had purchased a whole pallet of these tanks, and one of the guys brought two to our LDS to see if he could make doubles out of them. I not only told him that he could not, I also went to the school, and found the welding instructor who had made the purchase to practice welding on aluminum, and he agreed to drill each cylinder. John
|
|
|
Post by technidiver on Jun 27, 2019 16:29:39 GMT -8
Thanks for the photos John. Excellent reading as always. I did see the crack, but it slipped my mind how that could be detrimental to the performance. Was the plug welded in? It wasn't plugged in with Teflon and a bushing ever was it?
TD
|
|
|
Post by SeaRat on Jun 27, 2019 16:54:28 GMT -8
TD,
I don't know how the plug was inserted onto the cylinder; I kinda assume it was welded, but have no real info on that.
John
|
|
|
Post by luis on Jun 27, 2019 17:26:09 GMT -8
I am sorry John,
We have already talked about the testing of these cylinder. You can clearly read the stamped test pressure (TP) of 5000 psi.
The testing is also clearly spelled out in the cylinder procurement specifications. These cylinders are covered under MIL-C-24316.
I also take a big issue about you saying that a US Navy engineer would put out a specification for a pressure vessel that cannot be hydro tested. That is almost insulting to any engineer, but specially to a US Navy engineer.
Hydro testing is a requirement for any and all pressure vessels. That is basic OQE (Objective Quality Evidence) when accepting pressure vessels from any contractor or vendor. Our US Navy would never accept anything less.
I can guaranty you that the US Navy would never hire any engineer that would even consider putting out a specification for a pressure vessel that cannot be tested. That would be totally unsafe and irresponsible.
Hydro testing is the most basic OQE that is expected from any pressure vessel. The Navy buying a pressure vessel without the most basic OQE it would be totally irresponsible.
|
|
|
Post by luis on Jun 27, 2019 17:36:17 GMT -8
deleted
|
|
|
Post by technidiver on Jun 27, 2019 17:58:11 GMT -8
I am sorry John, We have already talked about the testing of these cylinder. You can clearly read the stamped test pressure (TP) of 5000 psi. The testing is also clearly spelled out in the cylinder procurement specifications. These cylinders are covered under MIL-C-24316. I also take a big issue about you saying that a US Navy engineer would put out a specification for a pressure vessel that cannot be hydro tested. That is almost insulting to any engineer, but specially to a US Navy engineer. Hydro testing is a requirement for any and all pressure vessels. That is basic OQE (Objective Quality Evidence) when accepting pressure vessels from any contractor or vendor. Our US Navy would never accept anything less. I can guaranty you that the US Navy would never hire any engineer that would even consider putting out a specification for a pressure vessel that cannot be tested. That would be totally unsafe and irresponsible. Hydro testing is the most basic OQE that is expected from any pressure vessel. The Navy buying a pressure vessel without the most basic OQE it would be totally irresponsible. Are these cylinders still in use by the navy? I know for a fact that Conshelfs, Solid Bar Manifolds, and Horsecollar BCDs are still used. TD
|
|
|
Post by luis on Jun 27, 2019 18:08:46 GMT -8
No, they are using modern aluminum 80's as doubles.
I saw bunches of them at the dive school in Panama city.
|
|
|
Post by SeaRat on Jun 27, 2019 19:04:23 GMT -8
I am sorry John, We have already talked about the testing of these cylinder. You can clearly read the stamped test pressure (TP) of 5000 psi. The testing is also clearly spelled out in the cylinder procurement specifications. These cylinders are covered under MIL-C-24316. I also take a big issue about you saying that a US Navy engineer would put out a specification for a pressure vessel that cannot be hydro tested. That is almost insulting to any engineer, but specially to a US Navy engineer. Hydro testing is a requirement for any and all pressure vessels. That is basic OQE (Objective Quality Evidence) when accepting pressure vessels from any contractor or vendor. Our US Navy would never accept anything less. I can guaranty you that the US Navy would never hire any engineer that would even consider putting out a specification for a pressure vessel that cannot be tested. That would be totally unsafe and irresponsible. Hydro testing is the most basic OQE that is expected from any pressure vessel. The Navy buying a pressure vessel without the most basic OQE it would be totally irresponsible. Luis, Your argument is with Bill High, not me. But to get to your argument, the U.S. Navy needed an antimagnetic Scuba at a time when there was no accepted technology for making aluminum high pressure cylinders. I'll do a bit more research and get back to you. John
|
|
|
Post by SeaRat on Jun 27, 2019 19:56:54 GMT -8
|
|
|
Post by luis on Jun 28, 2019 4:33:11 GMT -8
What Bill High was trying to say is that non-DOT cylinders cannot be re-qualified (as DOT cylinders) using hydro testing as if they were DOT cylinders.
You can hydro test any pressure vessel. You just can’t stamp the DOT license number on it. The hydro test facility DOT license number is the 4 digit code (one letter and three numbers) that is stamped with the hydro test date (between the month and the year).
These cylinders fall under the same situation as foreign cylinders. A lot of dive shops and even hydro test facilities will tell you that foreign cylinders cannot be hydro tested in the US. That is incorrect.
Many foreign commercial ships have life rafts with CO2 cylinders that get serviced while they are in US ports. The cylinders get hydro tested and stamped with just the date, not the DOT license number. As long as the cylinder is not used for commerce inside the US that is perfectly legal and I have seen many of them that come through Portland harbor.
Bill High was trying to teach to dive shop operators, many of them do not have any technical background. He just over simplified a statement. What he was trying to say is that hydro testing these cylinders will not make them legal in the US, so don’t bother hydro-ing them. Note: DOT jurisdiction is a separate subject.
The US Navy does not have to comply with DOT regulations just like it does not have to comply with Coast Guard regulations. In most cases it not only complies, but surpass some of the CFR (Code of Federal Regulations).
These cylinders were hydro tested on a regular basis by the Navy.
Your post clearly talks about hydro testing to 5000 psi with a periodicity of every 3 years. I am not sure what are you arguing.
Seriously… why are we having this debate again! You are posting stuff that clearly says that the Navy hydro tested them. Some of these debates go back to threads in 2006. I have wasted enough time.
I am sorry. It just hits a nerve for you to post that the US Navy would ever consider doing something as unsafe as operating pressure vessels without first testing them.
BTW, the correct term is non-magnetic. Not anti-magnetic. I realize that anti-magnetic has been used many times, but it is not accurate. Aluminum is non-magnetic.
|
|
|
Post by nikeajax on Jun 28, 2019 8:10:50 GMT -8
John, I'm not at all saying you're wrong about the crack: 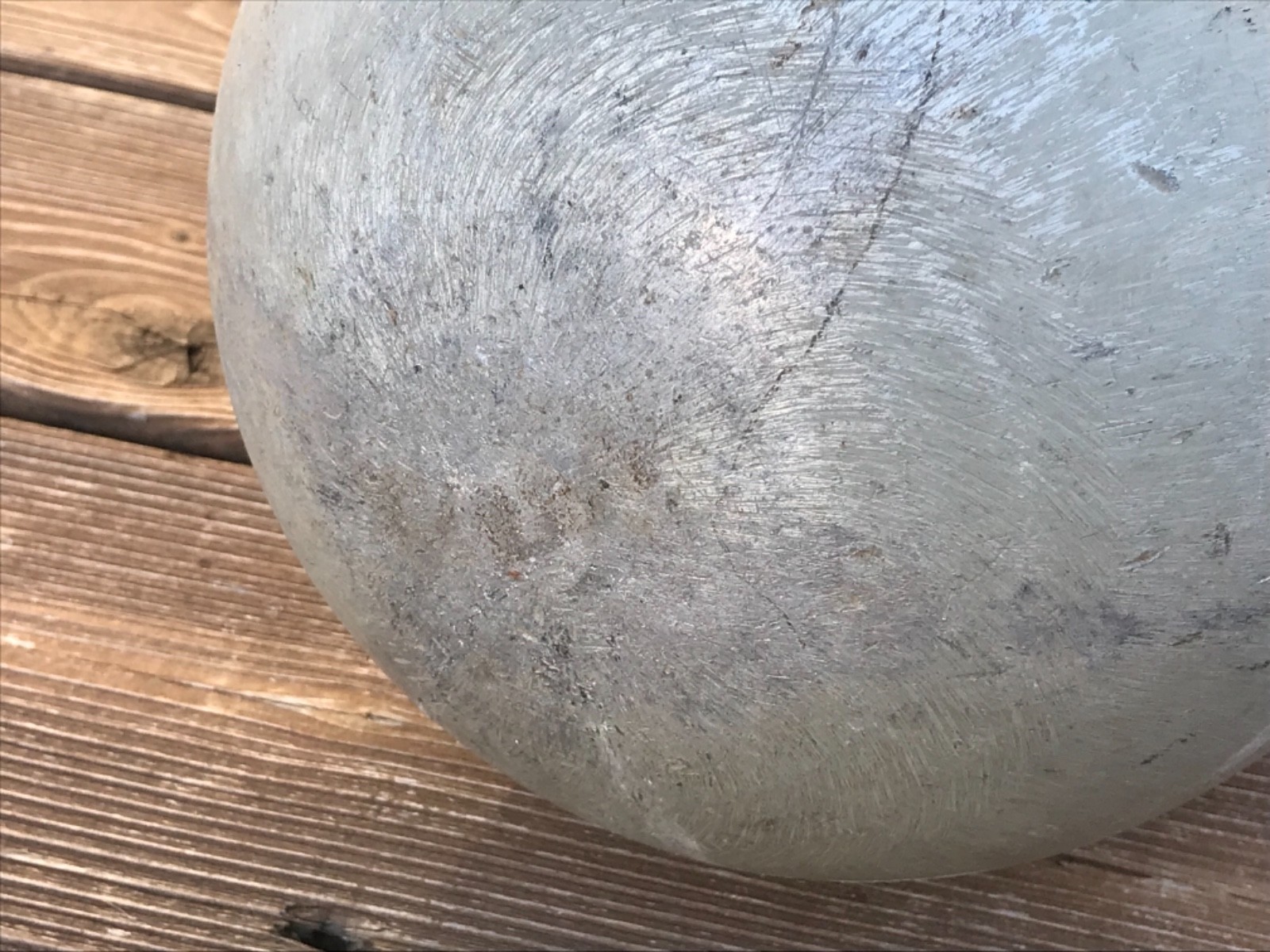 as it very well may be: that seems like a peculiar place for a crack to start don't it? All of the failed tanks I've seen at Steele's, the cracks are always in the neck  JB
|
|
|
Post by SeaRat on Jun 28, 2019 8:18:13 GMT -8
Okay Luis, I have made a change, and added a note above about the hydrostatic testing. I have also done some more research, and found this page which details what can be hydrostatic tested legally. www.law.cornell.edu/cfr/text/49/180.209I don't see these cylinders ("T.P. 3000") mentioned in the Table 1, Requalification of Cylinders; nor do I see them mentioned in any exception or special permet. Let me ask a question: Is there a difference between a pressure test to 5000 psig by the U.S. Navy and a hydrostatic test? My understanding is that, with a hydrostatic test, the cylinder is filled mostly with water, then tested. I may be wrong about that, but then, why use the word "hydro" in the testing process? To me that is different than the Navy using a pressure test, but I may have a misunderstanding about that. I was not intending to impune the U.S. Navy about having these cylinders made. What I was trying to say is that these cylinders have seen their useful life, and need to be discarded. By the way, I have done that with my other AL cylinders; none of them are now in service, even though I could have them hydroed and placed back into service. I just don't like the sustained-load cracking issue with the threads of these cylinders (I currently have four in my shed). John PS--JB, I saw that crack, and mentioned it. I simply don't know. But, you've never seen a cylinder manufactured by this process.
|
|
|
Post by luis on Jun 28, 2019 9:56:50 GMT -8
Again, these are not DOT cylinders. The Navy doesn’t have to comply with the DOT, but it does have its own safety programs. You will also not find foreign cylinders in that list. Foreign code cylinders are just a safe as our cylinders, but they are not allowed for commerce in the US.
Using air or any other compressible fluid (any gas) for high pressure testing is very risky and can be very dangerous if here is any possibility of failure. The stored compressed energy could destroy most testing facilities if there is a catastrophic failure of a pressure cylinder being tested (the size of a scuba tank). Therefore, all high pressure testing (in the Navy and industry) is always evacuated of any gas and filled with water or oil. By definition that is hydro testing. Even pressure testing of piping systems on a ship or submarine are always hydro tested. If at all possible, you always pressure test with a non-compressible fluid (a liquid). The maximum air pressure testing that I am aware of is ship compartment testing and that is to a maximum of 2 psi. More than that is considered dangerous. Compartment testing is mostly checking for leaks.
In the case of all high pressure cylinders like these scuba or even the foreign CO2 cylinders, they are totally filled with water. No air trapped in any part of the system is allowed. They are then placed inside a water jacket. The water jacket is only to measure the expansion by measuring the displaced water. The displaced water runs up a burette. Opposite to what some people think, the water jacket is not intended to absorb any energy in the case of a rupture. Since water is incompressible, the water just transmits the pressure out. The water jacket container has a large safety rupture disc (about 8” or 10” in diameter). In MIL-C-24316it calls out to follow the same CGA (Compress Gas Association) hydro test procedure used by most DOT cylinders. The test pressure of most cylinders is 5/3 of the working pressure. In other words for a working pressure (WP)of 3000 psi. the testing pressure (TP) is 5000 psi. The reason for this is that the allowable design working pressure for most alloys used in pressure vessels is 60% of yield. IN other words, the test pressure is at the low/ starting range of the yield stress. The reason to measure expansion is to check for the elastic expansion and any residual permanent plastic deformation.
BTW, the forming method used for these cylinders is just a spun process similar to the way the neck on all other cylinders is done. Asahi steel cylinders from Japan are made using a very similar process for both the neck and the bottom.
|
|
|
Post by nikeajax on Jun 28, 2019 9:57:48 GMT -8
John, it's my understanding, and I may be wrong, but the "hydro" part is they fill the tank with air, but in a water tank, and they see how much the tank displaces water. Again, I can/may be wrong. Also, I didn't expect you to know about the crack, I was just pointing it out is all: this place is as dead as a morgue as of late and merely trying to make conversation  JB
|
|